熱點資訊
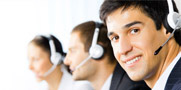
咨詢熱線:
0513-81100618
13861988658
郵件: linkai@ntcygs.cn
電話:13861988658
地址: 江蘇省南通市通州區(qū)張芝山鎮(zhèn)
熱門標簽
多層股鋼絲繩直線張拉狀態(tài)下接觸磨損機理研究
發(fā)布時間:2021-03-25 14:51 文章來源:未知 文章作者:admin 點擊數(shù):
摘 要:為了解多層股鋼絲繩內(nèi)部接觸磨損情況,通過不同方法對其在直線張拉狀態(tài)下的力學特性進行了研究。基于Costello 的普通鋼絲繩彈性理論,建立了拉力作用下直線狀態(tài)鋼絲繩的受
摘 要:為了解多層股鋼絲繩內(nèi)部接觸磨損情況,通過不同方法對其在直線張拉狀態(tài)下的力學特性進行了研究。基于Costello 的普通鋼絲繩彈性理論,建立了拉力作用下直線狀態(tài)鋼絲繩的受力模型,以18×7+IWS 多層股鋼絲繩為例,計算得出多層股鋼絲繩不同層繩股的應(yīng)力變化情況;根據(jù)鋼絲繩的空間幾何結(jié)構(gòu),分析鋼絲在接觸狀態(tài)下的受力情況,研究了鋼絲接觸應(yīng)力的大小和鋼絲間的滑動位移量對鋼絲接觸狀態(tài)和鋼絲疲勞磨損的影響;利用Abaqus 對鋼絲繩進行有限元靜力學分析,研究了繩股鋼絲間的應(yīng)力變形情況;最后在DIC-MTS 試驗臺進行了鋼絲繩直線狀態(tài)下的拉伸實驗,從力學角度分析了多層股鋼絲繩疲勞損傷的主要原因,對上述理論分析進行了驗證,并得出了多層股鋼絲繩在使用中其失效先從內(nèi)部磨損開始,繼而擴展斷裂的結(jié)論。
關(guān)鍵詞: 多層股鋼絲繩;相對錯動位移量;接觸應(yīng)力;疲勞磨損;DIC-MTS 拉伸實驗
中圖分類號:TH532 文獻標識碼:A 文章編號:1001-0785(2020)09-0032-06
0 引言鋼絲繩能夠改變力的傳遞方向,強度高、韌性好、抗沖擊,因此被廣泛用作多領(lǐng)域各類機械裝置的傳動件,并且很難被其它現(xiàn)有結(jié)構(gòu)件取代。鋼絲繩工作過程中受力情況復(fù)雜,因而失效形式多樣,其中內(nèi)部斷絲等通常難以通過常規(guī)外觀檢測方法發(fā)現(xiàn)[1]。多層股鋼絲繩在實際使用過程中,內(nèi)部鋼絲間的接觸磨損相較外部鋼絲間的接觸磨損要嚴重得多。因此,研究多層股鋼絲繩內(nèi)部接觸磨損情況是其磨損失效研究的重點,能為多層股鋼絲繩安全使用及結(jié)構(gòu)改善提供有力的理論支撐。
1 直線狀態(tài)鋼絲繩的應(yīng)力特性分析1.1 鋼絲繩鋼絲拉應(yīng)力在計算直線狀態(tài)下鋼絲拉應(yīng)力時,不考慮泊松比,即vi,vj 的值均取零[2],故第k 層單根鋼絲拉應(yīng)力為[3-5]

式中:F 為整繩所受拉力;ns 為繩股總層數(shù);j 為繩股所在層數(shù),j=0 時表示芯股;mj 為第j 層繩股的繩股總根數(shù);βj 為第j 層繩股的捻角;ng 為第j 層單個繩股中鋼絲的總層數(shù);mij 為第j 層繩股中第i 層鋼絲的總根數(shù);β ij 為第j 層繩股中第i 層鋼絲的捻角。
以18×7+IWS 多層股鋼絲繩為例,假定鋼絲繩受到F=15 kN 外部載荷作用,則鋼絲繩各繩股中的鋼絲拉應(yīng)力可由式(1)計算得出,具體數(shù)值見表1。

從表1 可以看出,鋼絲所受拉伸應(yīng)力隨所在繩股位置靠內(nèi)而增加;各繩股中外側(cè)鋼絲受到的拉伸應(yīng)力均比中心鋼絲小,鋼絲拉伸應(yīng)力與整繩所受拉伸載荷間關(guān)系如圖1 所示。由于在拉伸載荷作用下各層鋼絲伸長量不同,繩股間會出現(xiàn)相對滑動,導(dǎo)致分層現(xiàn)象。
1.2 內(nèi)、外層股鋼絲間接觸應(yīng)力根據(jù)Costello[6] 接觸理論,忽略接觸點的變形,由單股鋼絲繩接觸均勻載荷公式導(dǎo)出多層股鋼絲繩內(nèi)、外層股之間的接觸均布載荷計算公式為

圖1 18×7+IWS 多層股鋼絲繩鋼絲拉伸應(yīng)力隨拉伸載荷變化曲線內(nèi)、外層股鋼絲之間最大接觸應(yīng)力為其中


18×7+IWS 多層股鋼絲繩的內(nèi)、外層股捻距分別為90 mm 和170 mm 時,若外層股捻向為右交互捻,在所受拉伸載荷為15 kN 時,內(nèi)、外層股鋼絲間接觸應(yīng)力的計算值為-431.87 MPa。這一數(shù)值在鋼絲繩所受各類應(yīng)力中相對較大,可以認為是多層股鋼絲繩內(nèi)部接觸磨損的重要誘因之一。計算鋼絲接觸應(yīng)力隨捻距的變化情況,可以發(fā)現(xiàn)鋼絲接觸應(yīng)力隨鋼絲繩內(nèi)、外層股捻距的增大而遞減。因此,可以通過適當增大內(nèi)、外層股捻距改善多層股鋼絲繩內(nèi)部磨損情況,提高使用壽命。
1.3 鋼絲繩內(nèi)鋼絲間相對位移鋼絲繩中第j 股第i 絲層鋼絲的伸長量為

鋼絲繩中第j 股第i 絲層鋼絲的伸長量與其所受拉力的關(guān)系為

式中:△ Fij 為在拉伸過程中鋼絲拉力的變化量,△F ij =F ijmax -F ijmin;△Dij 為因第j 股第i 絲層鋼絲的拉伸變形引起與相鄰鋼絲之間的錯動位移量。
本文認為接觸磨損和接觸疲勞是由鋼絲繩拉伸變形引起的接觸應(yīng)力和鋼絲滑動位移量所導(dǎo)致的。因此,在第j 股同一層鋼絲的捻角和變形量均一致,鋼絲間的相對位移量近似為0;不同鋼絲層的鋼絲由于不同的捻角和變形量而導(dǎo)致不同的相對位移,可通過式(6)得到。
2 18×7+IWS 多層股鋼絲繩仿真分析2.1 鋼絲繩直線狀態(tài)幾何模型多層股鋼絲繩構(gòu)造呈現(xiàn)出復(fù)雜的空間螺旋結(jié)構(gòu),如圖2 所示。芯股中心鋼絲是一條直線,芯股外側(cè)鋼絲以一次空間螺旋線形式纏繞在中心鋼絲上;外側(cè)繩股(內(nèi)層股和外層股)中心鋼絲以一次空間螺旋線的形式圍繞芯股纏繞,外側(cè)繩股中的外側(cè)鋼絲以二次空間螺旋線形式纏繞在芯股上[7]。根據(jù)空間幾何學和Frenet 標架等數(shù)學知識推導(dǎo)出18×7+IWS 多層股鋼絲繩中任意一根鋼絲的空間螺旋線的表達式[8],輸入Pro/E 軟件中即可通過數(shù)學函數(shù)建模功能直接建立實體模型。

(a)螺旋結(jié)構(gòu)簡圖

(b)鋼絲繩示意圖圖2 直線狀態(tài)鋼絲繩示意圖
2.2 有限元仿真結(jié)果及分析直線狀態(tài)下18×7+IWS 多層股鋼絲繩承受大小為的15 kN 軸向載荷時Abaqus 有限元仿真結(jié)果見圖3a。鋼絲等效應(yīng)力在不同繩股鋼絲接觸區(qū)域附近達到峰值,內(nèi)、外層股鋼絲接觸點處等效應(yīng)力值達到508.3 MPa,與理論計算值431.78 MPa 有一定的偏差。仿真變形云圖見圖3b,加載端變形量最大,遠離加載端時鋼絲變形量逐漸減小最終趨于穩(wěn)定。

(a)等效云圖

(b)變形云圖圖3 等效云圖和變形云圖
同一橫截面上鋼絲變形量之差稱為鋼絲間錯動位移量[9],統(tǒng)計鋼絲繩芯股與內(nèi)層股、內(nèi)層股與外層股接觸區(qū)域選取加載端鋼絲及變形量變化圖如圖4 所示,不同層繩股接觸鋼絲間錯動位移由外而內(nèi)逐漸增加,且均遠大于同層繩股接觸鋼絲間錯動位移。

(a)芯股與內(nèi)層股兩接觸鋼絲伸長量

(b)內(nèi)層股兩相接觸側(cè)鋼絲伸長量

(c)內(nèi)層股股與外層股兩接觸鋼絲伸長量

(d)外層股兩相接觸側(cè)鋼絲伸長量圖4 相接觸鋼絲伸長量
3 鋼絲內(nèi)部磨損演化分析由前述可知,多層股鋼絲繩在直線狀態(tài)受到拉伸載荷時,鋼絲間會發(fā)生錯動位移,導(dǎo)致鋼絲的磨損,這種磨損在內(nèi)層股與外層股接觸鋼絲之間最為劇烈,嚴重時會導(dǎo)致斷絲使鋼絲繩失效。因此,研究鋼絲繩內(nèi)部磨損的演化過程,對了解由內(nèi)部磨損引起的鋼絲繩斷絲與疲勞失效具有重要意義[10]。
鋼絲內(nèi)部磨損過程中,因接觸鋼絲間的接觸應(yīng)力與鋼絲間錯動位移量的不同,磨損痕跡也不盡相同。鋼絲內(nèi)部磨損初期時鋼絲表面只有淺顯的摩擦痕跡,對鋼絲的受力與使用影響不大;當接觸鋼絲間接觸應(yīng)力較大而鋼絲相對錯動位移較小時,容易出現(xiàn)深度較深的馬鞍形磨損痕跡,隨著鋼絲內(nèi)部磨損的不斷加深,鋼絲的有效承載面積不斷減小,應(yīng)力集中情況愈發(fā)嚴重,直至發(fā)生鋼絲斷絲,這種情況常見于內(nèi)層股與外層股的接觸鋼絲之間,因為內(nèi)、外層股接觸鋼絲間接觸應(yīng)力最大且相對錯動位移量也較高。當接觸鋼絲間接觸應(yīng)力較小而鋼絲間相對錯動位移較大時,內(nèi)部鋼絲表面容易細長且深度較淺的磨損痕跡。
接觸鋼絲在不斷的磨損過程中,當內(nèi)、外層股接觸鋼絲的接觸角為φ 時,接觸處會產(chǎn)生馬鞍形的磨損,此時磨損量可用磨損體積近似值表示[11],即

式中:h 為最大磨損深度;φ 為接觸處鋼絲夾角;r1 為接觸區(qū)域內(nèi)層股鋼絲半徑;r2 為接觸區(qū)域外層股鋼絲半徑。本文所選18×7+IWS 多層股鋼絲繩r1= r2= r,即表達式可改寫為

在多層股鋼絲繩磨損的模擬研究中,Archard 模型與實際情況更為契合,故將其用于鋼絲繩接觸磨損程度的計算[12],即

式中:karc 為磨損系數(shù);△S 為鋼絲錯動位移; F c 為接觸載荷。由上式可推導(dǎo)出有關(guān)磨損深度h 的演化公式

其中,磨損系數(shù)karc 為實驗參數(shù)。
4 DIC-MTS 拉伸試驗4.1 實驗設(shè)計疲勞磨損是導(dǎo)致鋼絲繩斷裂的主要因素之一,是鋼絲繩使用過程中大量存在的損傷形式,為研究多層股鋼絲繩的磨損規(guī)律,以18×7-26 mm 多層股鋼絲繩為試驗研究對象設(shè)計了該實驗。1)實驗原理 去除鋼絲繩中的污漬后將鋼絲繩表面噴上散斑,試驗開始后采集鋼絲繩在拉伸載荷作用下的一系列散斑圖像,通過Vic-3D 軟件對采集到的圖像進行分析得到鋼絲繩全場應(yīng)變分布。
2)試驗參數(shù) 試驗載荷為15 kN,實驗開始前先進行幾次預(yù)加載,消除殘余應(yīng)力;試驗臺每加、卸載一次作為一次試驗循環(huán),模擬鋼絲繩工作中鋼絲繩的拉伸受力;試驗總共進行5 次加、卸載,即5 次試驗循環(huán)。
3)檢測方法 在試驗過程中,高速相機拍攝下每時刻鋼絲繩的整體狀態(tài)圖,然后用軟件分析鋼絲繩的應(yīng)變。試驗循環(huán)結(jié)束后清除鋼絲繩中的污漬,拍照記錄下鋼絲繩鋼絲外觀,拍攝時注意以鏡頭垂直磨損面,并用標尺輔助以便真實記錄磨損區(qū)域形狀及大小。試驗結(jié)束后,拆分繩股,用光學顯微鏡觀察磨損區(qū)域并記錄。
4.2 拉伸應(yīng)變試驗結(jié)果及分析樣本鋼絲繩長500 mm,鋼絲繩加、卸載循環(huán)受力圖如圖5 所示。試驗數(shù)據(jù)可知整繩拉伸伸長量為0.441 4 mm, 繩長500 mm, 上下夾具夾持深度各100 mm 且需手動調(diào)節(jié),實際軟件視野內(nèi)380 mm,整繩應(yīng)變?yōu)?.161 5×10-3,圖6 為系統(tǒng)分析18×7+IWS 鋼絲繩整繩拉伸應(yīng)變變化圖。
圖6 中Average 表示系統(tǒng)整個分析區(qū)域內(nèi)鋼絲繩拉伸應(yīng)變變化,R 0 表示選中區(qū)域內(nèi)鋼絲繩拉伸應(yīng)變變化;系統(tǒng)分析得鋼絲繩整繩拉伸應(yīng)變?yōu)?.168 4×10-3;理論計算應(yīng)變?yōu)?.161 5×10-3,兩者誤差不超過4%,驗證了理論計算與試驗的準確性。

圖5 18×7+IWS 鋼絲繩加、卸載循環(huán)受力圖

圖6 18×7+IWS 鋼絲繩整繩拉伸應(yīng)變變化圖
圖7 為18×7+IWS 鋼絲繩兩繩股接觸區(qū)域應(yīng)變分析圖。圖7a 中從左到右取點依次為p 0、p 1、p 2,在圖7b 中,p 0、p 1 所在的兩根鋼絲相互接觸,應(yīng)變p 2> p 1> p 0,由于在兩繩股接觸區(qū)域存在接觸應(yīng)力外加兩鋼絲之間的錯動位移量,導(dǎo)致接觸區(qū)域鋼絲拉伸應(yīng)變要較小于同股其他區(qū)域內(nèi)鋼絲拉伸應(yīng)變。

(a)兩繩股接觸區(qū)域

(b)接觸區(qū)域應(yīng)變圖7 兩繩股接觸區(qū)域應(yīng)變分析
5 結(jié)論1)多層股鋼絲繩鋼絲接觸應(yīng)力隨鋼絲繩內(nèi)、外層股捻距的增大而遞減,適當改變繩股鋼絲在繩中的捻距,鋼絲的拉伸應(yīng)力、鋼絲間接觸應(yīng)力同樣改變。研究發(fā)現(xiàn)繩股中內(nèi)、外層股鋼絲接觸間的接觸應(yīng)力要遠大于繩股中鋼絲所受到的拉應(yīng)力,接觸應(yīng)力是對鋼絲繩影響較大的一個應(yīng)力,也是對鋼絲繩的內(nèi)部磨損有重要影響的因素之一。
2)多層股鋼絲繩不同層繩股接觸鋼絲間的相對錯動位移由外而內(nèi)逐漸增加,且均遠大于同層繩股接觸鋼絲間的相對錯動位移。對于多層股鋼絲繩來說,接觸鋼絲之間的相對錯動導(dǎo)致鋼絲之間的摩擦磨損,由于多層股鋼絲繩的外層股與內(nèi)層股接觸間鋼絲具有應(yīng)力水平最大的接觸應(yīng)力,且相對錯動位移較大,因此這部分區(qū)域比較容易產(chǎn)生斷絲,即多層股鋼絲繩在使用中其失效先從內(nèi)部磨損開始,繼而擴展斷裂。
參考文獻[1] 譚繼文. 鋼絲繩安全檢測原理與技術(shù)[M]. 北京:科學出版社,2009.[2] Czitary E.Seilschwebebahnen[M].Wien:Springer,1952.[3] Costello G A,Miller R E.Lay effect of wire rope [J].Journal of the Soil Mechanics and Foundation Engineering Division,ASCE,1979,105 (EMS):597-608.[4] Costello G A,Sinha S K.Static behavior of wire rope [J]. Journal of the Soil Mechanics and Foundation Engineering Division,ASCE,1977103 (EMS):1 011-1 022.[5] Pilkey W D.Formulas for stress, strain, and structural matrices[D].New Jersey:John Wiley & Sons,Inc.,2005.[6] Laura P A A,Rossit C A.Theory of Wire Rope : by George A.Costello,Second Edition pp.122,1997.Springer:New York,N.Y[J].Ocean Engineering,2001(3):343,344.[7] 陳德斌. 多層股阻旋轉(zhuǎn)鋼絲繩受力特性與疲勞失效機理研究[D]. 武漢:武漢理工大學,2016.[8] 徐承軍,羅會超,盧茹利.18×7+IWS 多層股阻旋轉(zhuǎn)鋼絲繩彎曲特性研究[J]. 武漢理工大學學報,2017(2):66-71.[9] Boresi A P,Schmidt R J,Sidebottom O.M.Advanced Me chanics of materials[M].New York:Wiley,1993.[10] 張德坤. 鋼絲的微動磨損及其損傷疲勞行為研究[M]. 徐州:中國礦業(yè)大學出版社,2005.[11] Warburton J,Bradford R.The progressive wear of tubes: The volumes of the intersections of cylinders with each other and with flats[J].Wear,1986,113:331-352.[12] McColl I R,Ding J,Leen S B.Finite element simulation and experimental validation of fretting wear[J].Wear,2004,256:1 114-1 127.